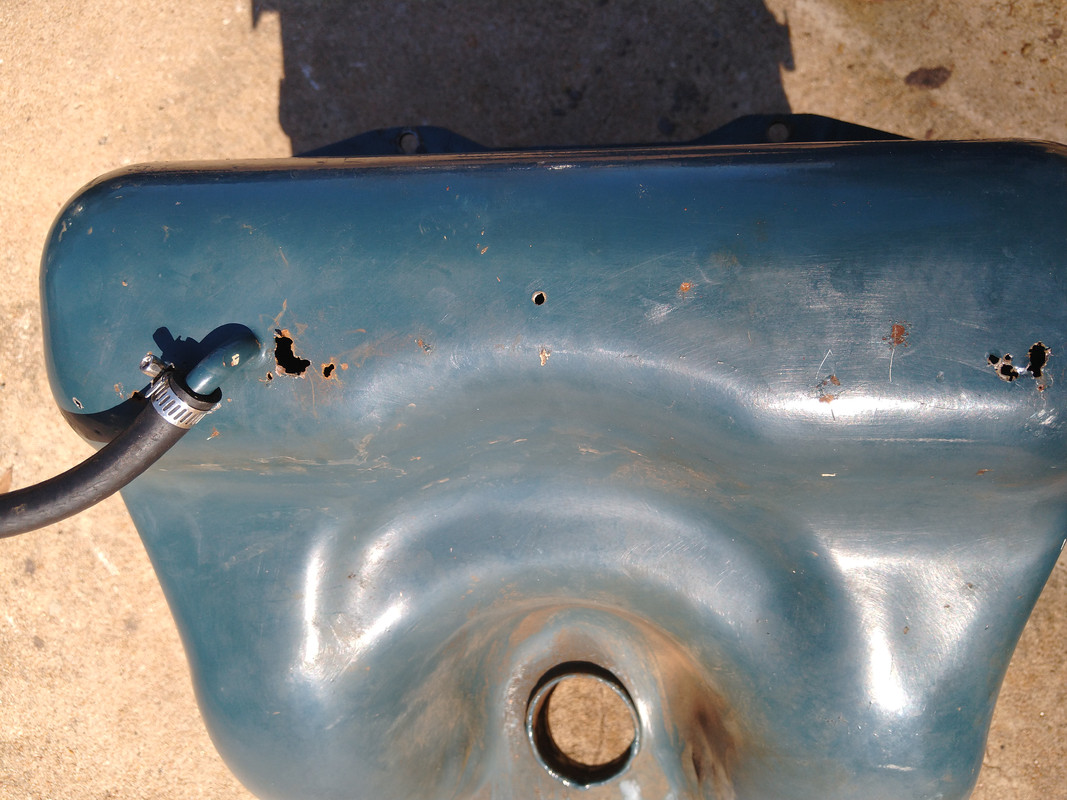
I've got rust holes in the bottom of a 40 year old Kubota tank. The holes shown in the picture are from after I cleaned the inside with E85, flushed it out, and dumped in a bunch of pea gravel to shake around in soap water to free up loose gunk on the inside, and then me probing with a pick and small screwdriver to expose any other weak metal. All hole that I've found are on the bottom.
Repair options I've seen mentioned are JB Weld Tank Repair, other epoxy repairs, & welding.
The JB Weld reviews have a number of people claiming it was only a temporary fix. Similar with other expoxies.
I have welding options (MIG & TIG); my skills are decent, but still amateur level. What I would like to do is cut a patch for each hole/area, bolt it in place, and then weld it all up, but I don't have an access hole large enough for my hand to work from the other side. I'd think if I tried to weld a patch from the outside, I'd end up burning through the thin metal.
The safest bet for me probably is to try the JB Tank repair, and if that fails, revisit this again. I'd sure like to get it right the 1st time though.
What would you do?