Neil.640.105091
New User
I am having a hard time finding what the
correct bolts to mount the under belly
bracket for a swinging draw bar.
In addition to that, I was disappointed to
discover that someone along the way had
sheard off 3 out of the 4 bolts. So I'm
also curious to know if I cant get the old
bolt extracted, would it be ok to use a
helicoil?
Thanks
correct bolts to mount the under belly
bracket for a swinging draw bar.
In addition to that, I was disappointed to
discover that someone along the way had
sheard off 3 out of the 4 bolts. So I'm
also curious to know if I cant get the old
bolt extracted, would it be ok to use a
helicoil?
Thanks
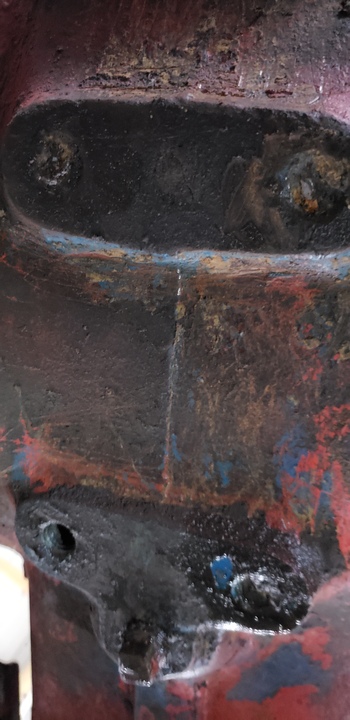