I've got a stuck bolt that I'm trying to remove, preferably without destroying the rubber bushing. I don't have a torch, which would likely be too much heat anyway, unless carefully applied directly to the bolt head. I do have a Lincoln AC225 and I've heard the old farmer's trick of thawing frozen metal pipes with the leads. Would this work with a bolt as well? I would think the welder setting should be relatively low?
I'm going to try the C-clamp/press from my ball joint kit first. I was able to get one side apart; the bolt is approximately 14mm diameter but only the first inch or so by the head and the rest of the shank is slightly smaller. What is the purpose of this design? I'm sure cheaper to manufacture as there's less material in the bolt but is there more logic to it than that? It seems like the smaller end would be a sloppy fit but also means it's only stuck for that first inch.
This isn't exactly what I'm working with but it's pretty close. My swaybar links are farther outboard and I would have to remove that to get the balljoint press in there. Due to control arm design, I have to come at it from the spindle side and that's where the swaybar link gets in the way.
I'm going to try the C-clamp/press from my ball joint kit first. I was able to get one side apart; the bolt is approximately 14mm diameter but only the first inch or so by the head and the rest of the shank is slightly smaller. What is the purpose of this design? I'm sure cheaper to manufacture as there's less material in the bolt but is there more logic to it than that? It seems like the smaller end would be a sloppy fit but also means it's only stuck for that first inch.
This isn't exactly what I'm working with but it's pretty close. My swaybar links are farther outboard and I would have to remove that to get the balljoint press in there. Due to control arm design, I have to come at it from the spindle side and that's where the swaybar link gets in the way.
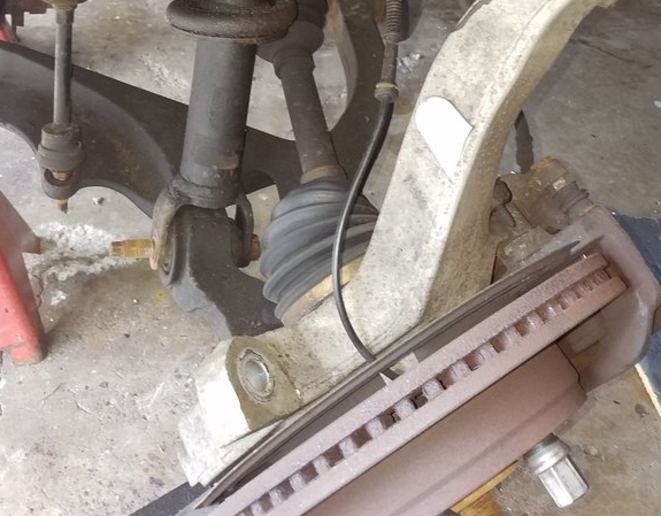